Seit 2020 hat die Wellpappenindustrie zahlreiche krisenhafte Ereignisse erlebt, die zu Engpässen, Verzögerungen und Preiserhöhungen bei Rohstoffen, Energie und Transport geführt haben. Die Pandemie hat zusammen mit Dürren und Stürmen in der westlichen Hemisphäre die Maisstärkeversorgung in Amerika abrupt beeinträchtigt; Der Krieg in der Ukraine wirkt sich auf die industrielle Stärkeproduktion in Europa aus ; Und die zunehmenden Spannungen in China und Korea haben zu weiteren Unterbrechungen in der Wellpappenbeschaffungskette geführt.
Read More >Apex International
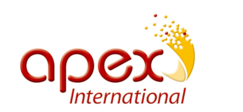
Recent Posts
Die Leimsatz-Lösung für einen unbeständigen Wellpappenherstellungsmarkt
GTT 2.0 liefert konsistenten Flexodruck
Apex International hat die Wiedereinführung der GTT-Anilox-Technologie angekündigt.
GTT 2.0 Anilox ist das Produkt von fast 10 Jahren Entwicklung und wurde speziell entwickelt, um Flüssigkeitsturbulenzen zu mildern, was zu einer ruhigen Flüssigkeitsoberfläche führt.
Read More >Apex International & Coveris White Ink-Projekt
Das Design und die Bildtreue von Verpackungen spielen eine Schlüsselrolle bei den Entscheidungen, die wir alle als Verbraucher treffen, was wiederum die Nachfrage antreibt.
Read More >Drei Wettbewerbsvorteile eines globalen Rasterwalzenherstellers
Nach Jahrhunderten des wirtschaftlichen und technologischen Fortschritts ist die Verpackungs- und Verarbeitungswelt mehr denn je vernetzt. Die Globalisierung hat sich auf alle Facetten unserer Branche ausgewirkt und seit Jahren Innovation und Zusammenarbeit über Grenzen hinweg gefördert. Für Verarbeiter, die in Flexo-, Beschichtungs- und Prägeanwendungen tätig sind, werden Sie möglicherweise feststellen, dass die Zusammenarbeit mit einem globalen Hersteller viele Wettbewerbsvorteile bietet, nicht nur für globale Verarbeiter, sondern auch für lokale Verarbeiter.
Read More >Probleme mit der Farbdeckung? So entscheiden Sie, ob Ihre Anilox überprüft werden sollte
Um der eigentlichen Ursache für Probleme von schlechter Farbdeckung auf den Grund zu gehen, müssen Sie sich einige Fragen stellen. Hier sind die drei häufigsten, um sicherzustellen, dass es keine Probleme mit Ihrem Druck gibt. Verwenden Sie dies als Leitfaden, um den besten Weg zur Behebung Ihres Abdeckungsproblems zu ermitteln.
Read More >Es gibt andere Möglichkeiten, Ihre Trocknungsprobleme zu beheben.
Der wahrscheinlich einfachste und schnellste Weg, um Probleme bei der Farbtrocknung während der Druckproduktion zu beheben, ist die Zugabe von trocknenden Lösungsmitteln zur Druckfarbe. Allerdings: In der Regel ist es nicht Ihre Farbe, die das Problem verursacht. Es könnte sich lohnen, einen anderen Ansatz zu wählen und zu verhindern, dass das Problem (erneut) auftritt.
Richtiges Arbeiten mit Wellpappe: Alles Sauber Halten!
Flexodrucker stehen Tag für Tag vor zahlreichen Herausforderungen – eine der größten ist oftmals der Flexodruckprozess selbst. Dies ist auf die zahlreichen beteiligten Variablen zurückzuführen. Und das Drucken auf Wellpappe macht es noch schwieriger, das gewünschte Ergebnis zu erzielen. Den Farbfluss konstant zu halten, ist der Schlüsselfaktor für ein richtiges Arbeiten.
Read More >Hauptursachen für Punktzuwachs durch Rasterwalzen
Punktzuwachs im Flexodruck hat vielerlei Ursachen und zeigt sich in vergrößerten Rasterpunkten bis hin zu deformierten Punkten, die mitunter unscharf ausdrucken können.
Read More >6 Richtlinien zur Verlängerung der Lebensdauer Ihrer Rasterwalze
Die Rasterwalze gilt als das Herzstück einer Druckmaschine. Während des Produktionsprozesses liegen die Toleranzen innerhalb von Mikrometern. Dies gilt für den Korpus, die Lager, die Zapfen und ebenso für die Keramikschicht auf der Oberseite sowie für die Lasergravurtechnologie, die das Volumen erzeugt. Sobald die Walze oder die Muffe an Sie geliefert wurde, gehen wir davon aus, dass Sie sie ebenfalls mit größter Sorgfalt behandeln, um eine möglichst lange Lebensdauer zu erzielen.
Read More >Vollständige Prozesskontrolle ist der Schlüssel zu konstanter Druckqualität
Der Etiketten- und Verpackungshersteller Reflex ist eines der größten Unternehmen seiner Art im Vereinigten Königreich: „Wir sind bestrebt, an der Spitze der Innovation zu stehen, indem wir in Technologie und Menschen investieren, um kontinuierlich besser zu werden.“ Um die Druckqualität in der Etikettenabteilung, die aus sieben Produktionsstätten mit mehreren Pressen besteht, zu standardisieren, ging Reflex eine Partnerschaft mit Experten von Apex ein, um eine bessere Prozesskontrolle zu erzielen.
Read More >SUBSCRIBE VIA EMAIL
POSTS BY TOPIC
- Flexo (14)
- Anilox (13)
- Rasterwalze (8)
- Flexography (7)
- anilox roll (6)
- Fixed Palette (5)
- Anilox Sleeve (4)
- Anilox Volume Measurement (4)
- Label (4)
- Apex (3)
- Etiketten (3)
- Farbe (3)
- Troika AniCAM (3)
- Troika Anilox Measurement (3)
- Volume Accuracy (3)
- 4c fixed palette (2)
- Accora (2)
- Anilox Lifetime (2)
- Bellissima (2)
- Corrugated (2)
- Corrugated Board (2)
- Druckplatten (2)
- ECG (2)
- Eliminierung von UV Spitting (2)
- Expanded Color Gamut (2)
- Flexible Verpackungen (2)
- GTT (2)
- UltraCell (2)
- Wellpappe (2)
- sleeve Anilox (2)
- 7C Fixed palette (1)
- Anilox Cleaning (1)
- Anilox Measurement (1)
- Anilox Press Installation (1)
- Anilox Training (1)
- Apex use and care guide (1)
- Bridging (1)
- Christian Huth (1)
- Dot gain (1)
- Farbspritzen (1)
- Flexo troubleshooting (1)
- GTT2.0 (1)
- Glue Sets (1)
- Labelexpo (1)
- Leimwalze (1)
- Luftzylinder (1)
- Lösungsmitteltinte (1)
- Microsoft Dynamics (1)
- Pantone simulation (1)
- REVO (1)
- RFID (1)
- Rastersleeve (1)
- Rastersleeve einbau (1)
- Reflex Group (1)
- Sleeve montage (1)
- Smart Anilox (1)
- Tintentrockneprobleme (1)
- Trocknungslösungsmittel (1)
- UV (1)
- digital flexo (1)
- flexographie (1)
- in-mould labels (1)
- opaque white (1)
- partnerschaft (1)
- rakelmesser (1)